Super Ceramic Sand for Sand Foundry
Features
• Uniform component composition
• Stable grain size distribution and air permeability
• High refractoriness (1825°C)
• High resistance to wear, crush and thermal shock
• Little thermal expansion
• Excellent fluidity and filling efficiency owing to being spherical
• Highest reclamation rate in the sand loop system
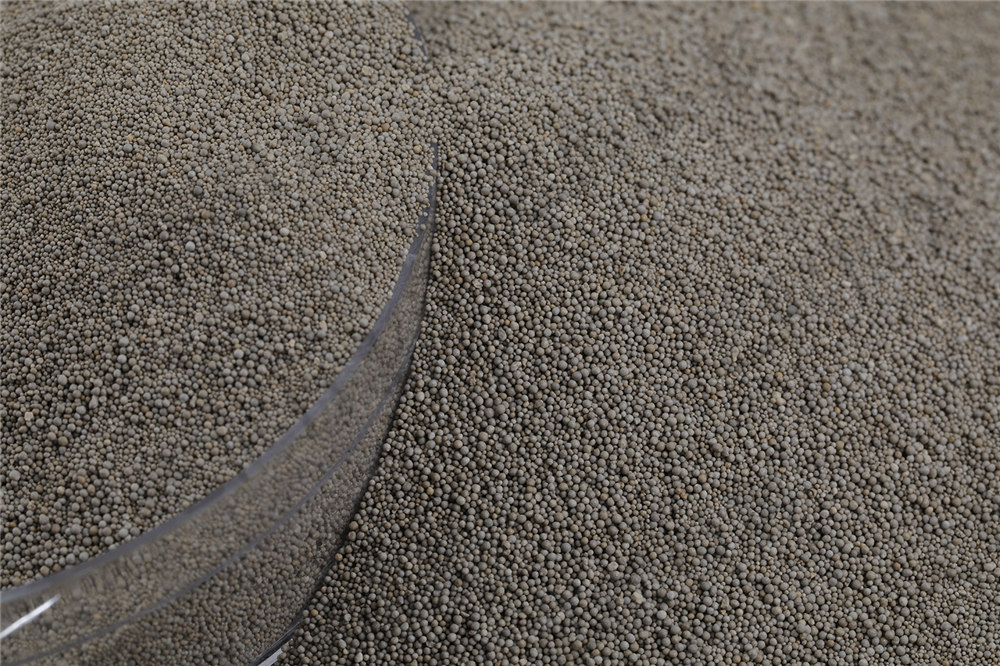
Application Sand Foundry Processes
RCS (Resin coated sand)
Cold box sand process
3D printing sand process (Include Furan resin and PDB Phenolic resin)
No-bake resin sand process (Include Furan resin and Alkali phenolic resin)
Investment process/ Lost wax foundry process/ Precision casting
Lost weight process/ Lost foam process
Water glass process
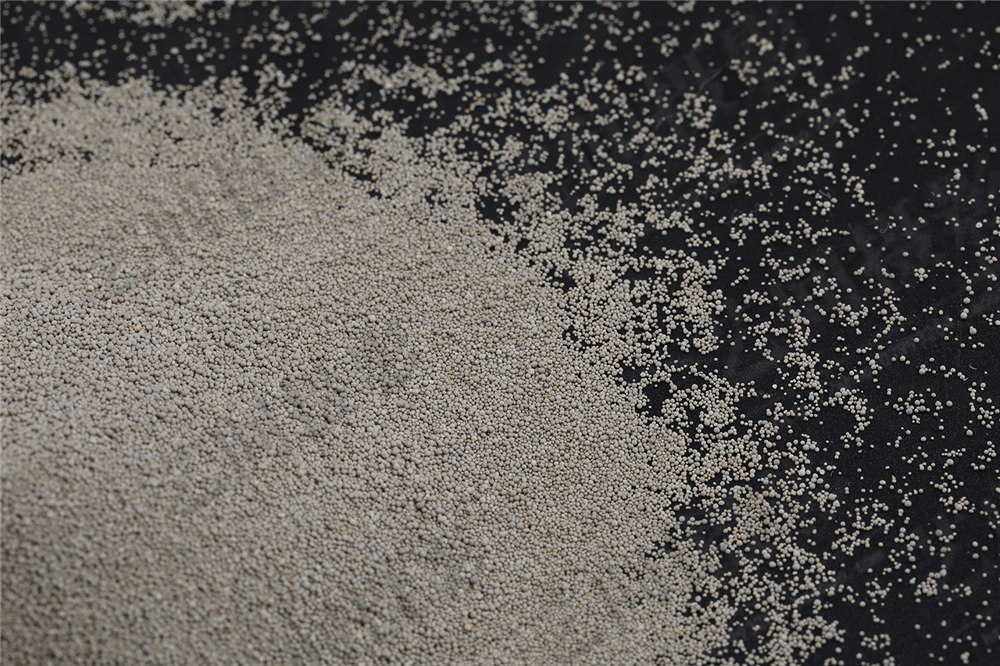
Ceramic Sand Property
Main Chemical Component | Al₂O₃ 70-75%,
Fe₂O₃<4%, |
Al₂O₃ 58-62%,
Fe₂O₃<2%, |
Al₂O₃ ≥50%,
Fe₂O₃<3.5%, |
Al₂O₃ ≥45%,
Fe₂O₃<4%, |
Produce process | Fused | Sintered | Sintered | Sintered |
Grain Shape | Spherical | Spherical | Spherical | Spherical |
Angular Coefficient | ≤1.1 | ≤1.1 | ≤1.1 | ≤1.1 |
Partical Size | 45μm -2000μm | 45μm -2000μm | 45μm -2000μm | 45μm -2000μm |
Refractoriness | ≥1800℃ | ≥1825℃ | ≥1790℃ | ≥1700℃ |
Bulk Density | 1.8-2.1 g/cm3 | 1.6-1.7 g/cm3 | 1.6-1.7 g/cm3 | 1.6-1.7 g/cm3 |
PH | 6.5-7.5 | 7.2 | 7.2 | 7.2 |
Application | Steel, Stainless steel, Iron | Steel, Stainless steel, Iron | Carbon steel, Iron | Iron, Aluminum, Copper |
Grain Size Distribution
Mesh |
20 | 30 | 40 | 50 | 70 | 100 | 140 | 200 | 270 | Pan | AFS Range |
μm |
850 | 600 | 425 | 300 | 212 | 150 | 106 | 75 | 53 | Pan | |
#400 | ≤5 | 15-35 | 35-65 | 10-25 | ≤8 | ≤2 | 40±5 | ||||
#500 | ≤5 | 0-15 | 25-40 | 25-45 | 10-20 | ≤10 | ≤5 | 50±5 | |||
#550 | ≤10 | 20-40 | 25-45 | 15-35 | ≤10 | ≤5 | 55±5 | ||||
#650 | ≤10 | 10-30 | 30-50 | 15-35 | 0-20 | ≤5 | ≤2 | 65±5 | |||
#750 | ≤10 | 5-30 | 25-50 | 20-40 | ≤10 | ≤5 | ≤2 | 75±5 | |||
#850 | ≤5 | 10-30 | 25-50 | 10-25 | ≤20 | ≤5 | ≤2 | 85±5 | |||
#950 | ≤2 | 10-25 | 10-25 | 35-60 | 10-25 | ≤10 | ≤2 | 95±5 |
Description
Super Ceramic Sand is a man-made spherical particle shape high-end foundry sand. Known by many names including Ceramic Sand, Cerabeads and CeramCast, an excellent choice for the sand casting industry.
One of the main advantages of super ceramic sand is its high refractoriness. In addition, the product has almost no thermal expansion, which means it retains its shape even when there are significant changes in temperature.
Super Ceramic Sand also has an excellent angle factor, which means it flows freely around complex shapes and intricate details. This makes it ideal for complex castings and molds.
Another impressive feature of Super Ceramic Sand is its high recovery rate. This means that the product can be reused many times, which not only reduces waste, but also saves production time and money. The high recovery rate also means the product is environmentally friendly as it minimizes the amount of material that needs to be mined and processed.
In conclusion, Super Ceramic Sand is a game changer for the sand foundry industry. With its high performance and exceptional durability, it is ideal for complex castings and molds. Its high recycling rate and environmental benefits make it a responsible and sustainable choice for manufacturers.