Mullite Ball Sand 60
Features
• Uniform component composition
• Stable grain size distribution and air permeability
• High refractoriness (1825°C)
• High resistance to wear, crush and thermal shock
• Little thermal expansion
• Excellent fluidity and filling efficiency owing to being spherical
• Highest reclamation rate in the sand loop system

Application Sand Foundry Processes
RCS (Resin coated sand)
Cold box sand process
3D printing sand process (Include Furan resin and PDB Phenolic resin)
No-bake resin sand process (Include Furan resin and Alkali phenolic resin)
Investment process/ Lost wax foundry process/ Precision casting
Lost weight process/ Lost foam process
Water glass process
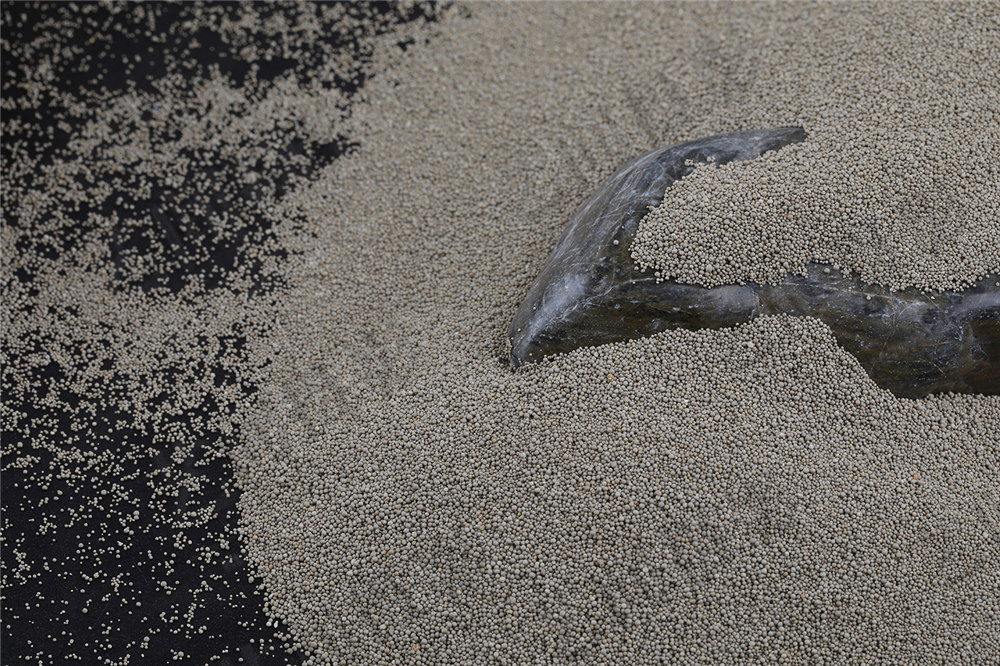
Advantage
Grandly launch the high-quality ceramic foundry sand - mullite ball sand 60, which is popular in the foundry industry! Known as ceramic sand in China and Cerabeads in Japan, this man-made sand is an extremely stable product with mullite crystals, making it ideal for making sand molds and cores for high-value products in metal casting.
If you've been in the foundry industry, you know the importance of having the right material to ensure the quality of your final product. When creating sand molds and cores, Mullite Ball Sand 60 is unmatched for its stability and durability. This sand is designed to provide exceptional quality and consistency for the core production process.
One of the most significant advantages of using Mullite Ball Sand 60 is that you can save up to 50% in binder compared to other sands, without sacrificing the strength of the core. This means cost savings for your business while maintaining optimum quality. Plus, its exceptional properties ensure your castings have a clean, smooth finish.
Additionally, the Mulite Ball Sand 60 is suitable for both small and large foundries, providing an efficient, hassle-free and cost-effective solution for their sand mold and core production processes. Its exceptional performance and reliability make it one of the most sought-after premium ceramic foundry sands on the market today.
Ceramic Sand Property
Main Chemical Component | Al₂O₃ 58-62%, Fe₂O₃<2%, |
Grain Shape | Spherical |
Angular Coefficient | ≤1.1 |
Partical Size | 45μm -2000μm |
Refractoriness | ≥1800℃ |
Bulk Density | 1.6-1.7 g/cm3 |
PH | 7.2 |
Grain Size Distribution
Mesh |
20 | 30 | 40 | 50 | 70 | 100 | 140 | 200 | 270 | Pan | AFS Range |
μm |
850 | 600 | 425 | 300 | 212 | 150 | 106 | 75 | 53 | Pan | |
#400 | ≤5 | 15-35 | 35-65 | 10-25 | ≤8 | ≤2 | 40±5 | ||||
#500 | ≤5 | 0-15 | 25-40 | 25-45 | 10-20 | ≤10 | ≤5 | 50±5 | |||
#550 | ≤10 | 20-40 | 25-45 | 15-35 | ≤10 | ≤5 | 55±5 | ||||
#650 | ≤10 | 10-30 | 30-50 | 15-35 | 0-20 | ≤5 | ≤2 | 65±5 | |||
#750 | ≤10 | 5-30 | 25-50 | 20-40 | ≤10 | ≤5 | ≤2 | 75±5 | |||
#850 | ≤5 | 10-30 | 25-50 | 10-25 | ≤20 | ≤5 | ≤2 | 85±5 | |||
#950 | ≤2 | 10-25 | 10-25 | 35-60 | 10-25 | ≤10 | ≤2 | 95±5 |