Ceramsite Sand
Features
• Uniform component composition
• Stable grain size distribution and air permeability
• High refractoriness (1800°C)
• High resistance to wear, crush and thermal shock
• Little thermal expansion
• Excellent fluidity and filling efficiency owing to being spherical
• Highest reclamation rate in the sand loop system
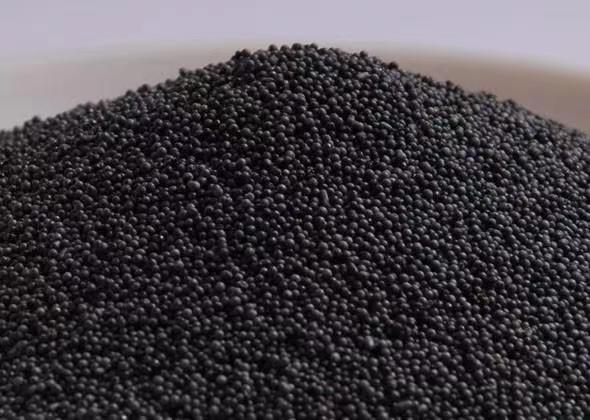
Application Sand Foundry Processes
RCS (Resin coated sand)
Cold box sand process
3D printing sand process (Include Furan resin and PDB Phenolic resin)
No-bake resin sand process (Include Furan resin and Alkali phenolic resin)
Investment process/ Lost wax foundry process/ Precision casting
Lost weight process/ Lost foam process
Water glass process
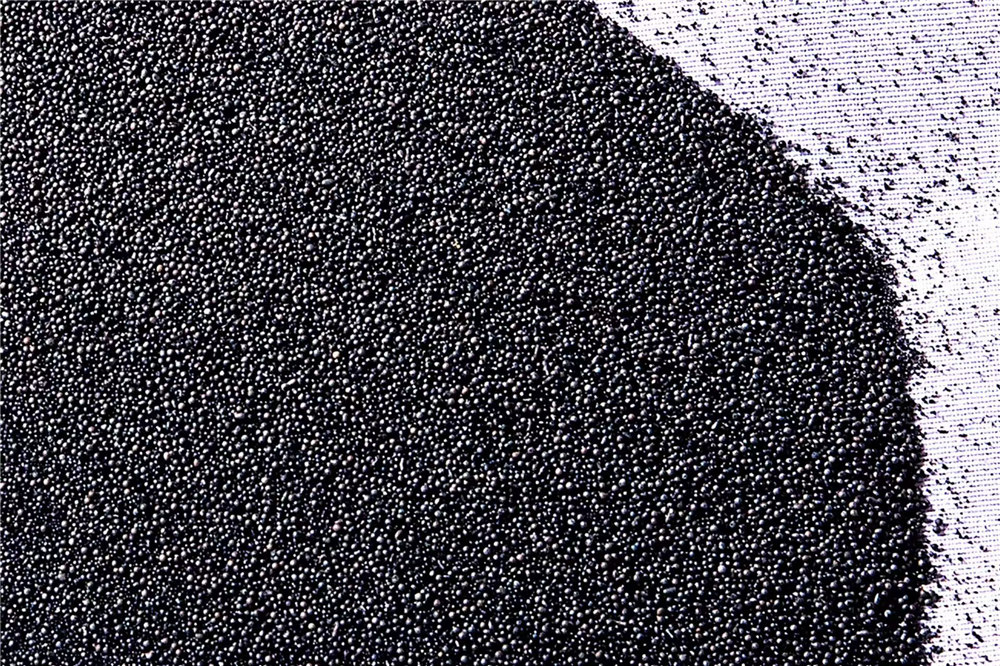
Ceramic Sand Property
Main Chemical Component | Al₂O₃ 70-75%,
Fe₂O₃<4%, |
Grain Shape | Spherical |
Angular Coefficient | ≤1.1 |
Partical Size | 45μm -2000μm |
Refractoriness | ≥1800℃ |
Bulk Density | 1.8-2.1 g/cm3 |
PH | 6.5-7.5 |
Application | Steel, Stainless steel, Iron |
Grain Size Distribution
Mesh |
20 | 30 | 40 | 50 | 70 | 100 | 140 | 200 | 270 | Pan | AFS Range |
μm |
850 | 600 | 425 | 300 | 212 | 150 | 106 | 75 | 53 | Pan | |
#400 | ≤5 | 15-35 | 35-65 | 10-25 | ≤8 | ≤2 | 40±5 | ||||
#500 | ≤5 | 0-15 | 25-40 | 25-45 | 10-20 | ≤10 | ≤5 | 50±5 | |||
#550 | ≤10 | 20-40 | 25-45 | 15-35 | ≤10 | ≤5 | 55±5 | ||||
#650 | ≤10 | 10-30 | 30-50 | 15-35 | 0-20 | ≤5 | ≤2 | 65±5 | |||
#750 | ≤10 | 5-30 | 25-50 | 20-40 | ≤10 | ≤5 | ≤2 | 75±5 | |||
#850 | ≤5 | 10-30 | 25-50 | 10-25 | ≤20 | ≤5 | ≤2 | 85±5 | |||
#950 | ≤2 | 10-25 | 10-25 | 35-60 | 10-25 | ≤10 | ≤2 | 95±5 |
Description
Ceramsite Sand, the revolutionary product that has transformed the foundry industry. Made from high quality calcined bauxite, this black ball shaped sand has been designed to provide superior performance in molding and core sand applications.
One of the key features of Ceramsite Sand is its almost perfectly spherical shape. This unique shape creates excellent flow characteristics and gas permeation, making it the ideal choice for both mold and core production. In fact, binder savings of up to 50% have been achieved compared to other sands, without any loss in core strength.
In addition to its superior molding and core sand properties, Ceramsite Sand for foundry use also delivers an excellent surface finish on castings. This, combined with its high refractoriness (1800°C) and resistance to wear, crush and thermal shock, makes it the go-to choice for a wide range of foundry applications.
But that's not all - Ceramsite Sand also boasts a stable grain size distribution and air permeability, coupled with little thermal expansion. This ensures that the sand remains uniform in composition, and provides excellent fluidity and filling efficiency.
And, with the highest reclamation rate in the sand loop system, Ceramsite Sand is not only efficient but also environmentally sustainable. It can be used again and again, resulting in significant cost savings for foundries over time.
In conclusion, Ceramsite Sand is a game changer in the foundry industry. Its unique properties and superior performance have revolutionized the way foundries operate, and it continues to be the preferred choice for foundries around the world. Try it for yourself and experience the benefits of Ceramsite Sand, the ultimate sand solution!